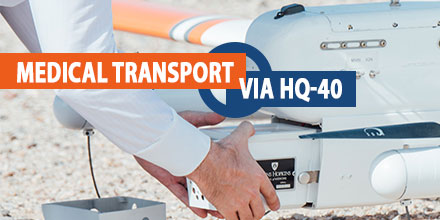
Researchers from John Hopkins University School of Medicine recently partnered with Latitude Engineering for a very unique study. The goal? To test the viability of transporting medical samples across 161 miles of Arizona desert via drone.
LatitudeEngineering's HQ-40 provided transport. The on-board payload system maintained temperature control throughout the three-hour long flight. This ensured the samples maintained viability for laboratory analysis upon landing.
The successful mission also set a new distance record for unmanned medical drone delivery.
Advanced report findings
A report, published ahead of print in the American Journal of Clinical Pathology, June edition, gave light to some interesting finding.
Accumulative evidence, investigators suggest, indicates that unmanned aircraft are an effective, safe and timely way to quickly transport medical samples from remote patients to laboratories with advanced diagnostic capabilities.
“Drone air transport will be the quickest, safest and most efficient option to deliver biological samples to a laboratory whether it be in a rural or urban setting,” says Timothy Amukele, M.D., Ph.D. “We don’t need to fix 20th Century problems, such as no roads, poor roads or driving vehicles through crowded urban streets to improve patient care. Logistical inefficiencies are an enemy of patient care. Drones will take patient care into the 21st Century by making patient diagnoses quicker and more efficient.”
Real world results
The study demonstrated real world long distance transport of samples involving several modes of transportation. The team collected 84 samples in pairs at the University of Arizona in Tucson and driven 76 miles to an airfield. One sample from each pair was loaded on the drone, which flew them 161 miles.
Following the flight, they transported all sample 62 miles to the Mayo Clinic in Scottsdale, Arizona. Finally, the team compared each pair of samples was to check for differences between the flown and not-flown sample.
Results from sample pairs were similar for 17 of the 19 tests. Small differences were seen in Glucose and Potassium, which do also vary in other transport methods. We suspect the differences seen in this test arose because the samples not-flown by drone were not as carefully temperature controlled as the flown samples in the temperature-controlled chamber.
Medical transport via drone
The aircraft used in this study was a Latitude Engineering HQ-40. The unique "quadplane" hybrid configuration of the craft enables it to take off vertically and transition to traditional horizontal flight. Due to its unique design, the HQ-40 can land in small spaces as well as fly efficiently between widely separated facility. This makes it a viable option for use at medical facilities.
The flight team took numerous precautions throughout the test. A certified remote pilot controlled the aircraft throughout the test which they performed in restricted airspace at a military aircraft test range cleared of all traffic. The flight team controlled the aircraft via a radio link between the on-board flight computer and the ground control station.
The team packed and transported the samples according to IATA guidelines.
During transport, the samples were in a temperature controlled chamber designed by the Hopkins team. The chamber used electrical power from the aircraft to maintain the samples at room temperature. The device is lighter than an equivalent amount of ice, the current method of temperature control. Additionally, the chamber can warm the samples in cold weather.
Building on previous work
Previously, the Johns Hopkins team studied the impact of drone transportation on the chemical, hematological, and microbial makeup of drone-flown blood samples. They found no negative affects on the samples. The test involved drone flight distances up to approximately 20 miles.
The new study examined the effects of drone transportation over longer distances, more than 160 miles, and significantly longer time periods that require environmental controls. The team plans further and larger studies in the U.S. and overseas.
“My vision is that we engage drone technology to fly over challenges presented by self-limiting ground transportation systems,” says Amukele. “So, our hospitals will have diagnostic results far more quickly. And, when a first responder arrives to the scene of an accident, he or she will be met by a medical delivery drone carrying the correct blood product. Together, we will most certainly improve care and save more lives.”
Authors of this study are include Timothy K. Amukele MD PhD, and Jeff Street, Department of Pathology, Johns Hopkins University School of Medicine. Christine LH Snozek PhD and James Hernandez MD, Department of Laboratory Medicine and Pathology, Mayo Clinic College of Medicine, Mayo Clinic in Arizona, Phoenix and Scottsdale, Arizona. Ryan G. Wyatt, Matthew Douglas MD, and Richard Amini MD, Department of Emergency Medicine, University of Arizona, Tucson, Arizona.
Peter Kovler of the Blum-Kovler Foundation provided funding for the study.
Find out more about the Johns Hopkins study,
here.